- Fast response times and short transport times in the event of battery damage
- Transfer of expertise within the company
- Standardised repair processes for all battery types of MAN electric commercial vehicles
- Battery Closed Loop contributes to achieving MAN’s sustainability goals as part of the Circular Economy Strategy: closed loop for batteries is the goal
In 2024 and 2025, MAN Truck & Bus will establish battery repair centres in Italy, Denmark/Norway, Austria, Belgium, Netherlands, France, Poland and UK, with further countries in Europe being planned. Millions will be invested in these centres over the next two years. Two battery repair centres are already in operation in Germany (Hanover-Laatzen site) and Spain (Barcelona). The roll-out of the battery repair hubs in Europe is necessary because the first units of the new MAN eTruck generation will be delivered to customers in 2024. Over 1,000 battery-electric MAN city buses and more than 2,400 all-electric MAN vans are already on Europe’s roads. With the ramp-up of MAN eTruck production, the electric vehicle population will continue to increase significantly in the coming years. The Munich-based commercial vehicle manufacturer is preparing intensively for this within its service organisation.
“Battery repair is a necessity for MAN in order to ensure the economic efficiency and operational readiness of our customers’ electric vehicles at a high level. We also make a major contribution to the closed-loop approach of traction batteries, as this extends the battery life in the vehicle, which conserves important resources,” says Christopher Kunstmann, Senior Vice President Customer Service Management at MAN Truck & Bus.
The first battery repair centre and the associated build-up of expertise in the repair of batteries dates back to 2020. The first pilot repairs and process documentation were carried out for the battery of the MAN eTGE electric van, which was launched on the market in 2018. This was followed by the battery packs of the MAN eTGM distribution truck, which was launched in a small series in 2020, and the start of series production of the MAN Lion’s City E electric city bus – also in 2020. Repair steps were trialled for all of these different batteries, employees were trained, repair instructions were created and workplace requirements were defined.
This knowledge, which was built up in the first MAN battery repair centre in Hanover-Laatzen, is now being successively transferred to the other markets. The aim is to operate a battery repair hub in every market in which MAN is represented with battery-electric commercial vehicles. Short transport routes and highly trained technicians on site will ensure that the battery can be repaired quickly. This minimises vehicle downtime.
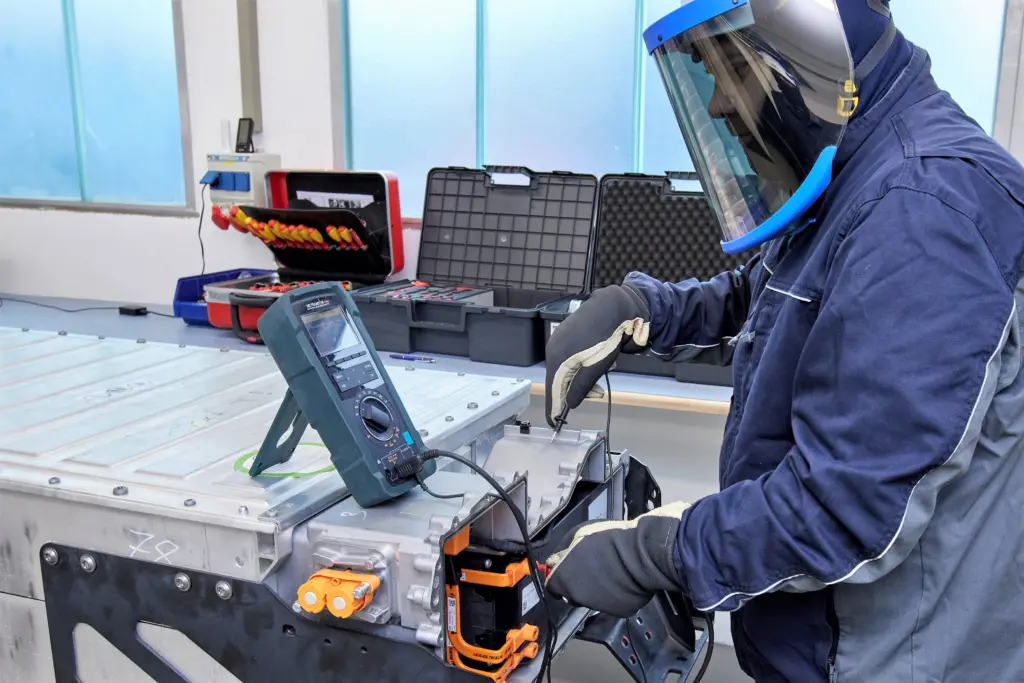
At MAN, a battery repair centre has to meet certain criteria based on practical experience and legal standards in the respective countries. On the one hand, the appropriate high-voltage and special tools are required for handling the respective battery types of the vehicles. In addition, special protective equipment must be available for the electricians working there. The premises also fulfil certain requirements, e.g. access control, double doors, air conditioning, ventilation concept, 400 V socket and load crane.
MAN Truck & Bus’s primary objective is to utilise the battery in the vehicle for as long as possible. That is why repair and remanufacturing are at the centre of current measures. Since 2023, MAN has been leading the REVAMP project, a consortium of nine partners from industry and science. This three-year project aims to automate the process of assessing the condition of used vehicle batteries. This knowledge will be used to remanufacture batteries economically so that they can then be used in vehicles (2nd use) or for other purposes (2nd life). The REVAMP project is funded by the Federal Ministry of Economics and Climate Protection (BMWK).
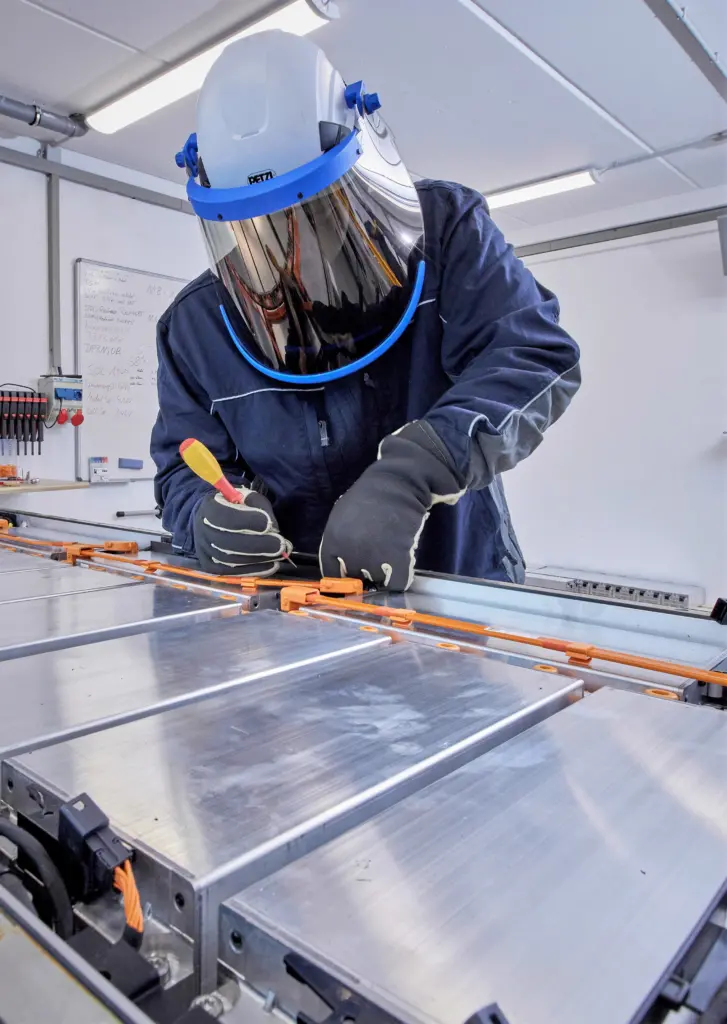
Repairing and reconditioning the battery are key elements of the Battery Closed Loop strategy and MAN’s sustainability strategy. The diagonal capability of the battery and its economical dismantling are essential for this. The overarching goal is to establish a closed loop for the batteries. Important milestones in this battery cycle are, after the first use in the vehicle, a further use in the vehicle (2nd use) or in another application (2nd life).
In order to close the closed loop of valuable battery materials, MAN is already focussing on recycling and the return of recycled raw materials (recyclate) into new battery cells. The growing demand for battery cells for the electrification of the MAN portfolio will increase greenhouse gas emissions in the supply chain unless dedicated measures are taken to counteract this. The use of secondary materials is one of the possible levers that need to be addressed in order to decarbonise the battery cell hotspot. In this way, we are also making a contribution towards achieving net-zero greenhouse gas emissions, which MAN has committed to in 2021 as part of the Science Based Targets initiative (SBTi).
The prerequisite for the battery closed loop is that sufficient recycled material is available. To ensure that this is the case in the future, MAN is currently working with its parent company TRATON SE and the COE (Centre of Excellence) at Volkswagen AG on concepts that will enable closed cycles. The aim here is to ensure that sufficient recyclate is available for new batteries in the future in order to meet the target values of the European Union’s new Battery Ordinance (BattVO).
In 2023, MAN Truck & Bus also became a partner of the Munich start-up network Circular Republic in order to move closer to the goal of the Battery Closed Loop. Circular Republic is part of UnternehmerTUM GmbH and has set itself the task of bringing established companies and start-ups together to implement and further develop innovations in the circular economy. In a first project under the leadership of Circular Republic, MAN is working together with other cooperation partners on the semi-automated dismantling of traction batteries and the recycling of cell modules.